ORiNの誕生と歩み:製造業界の通信標準化の起源と変遷
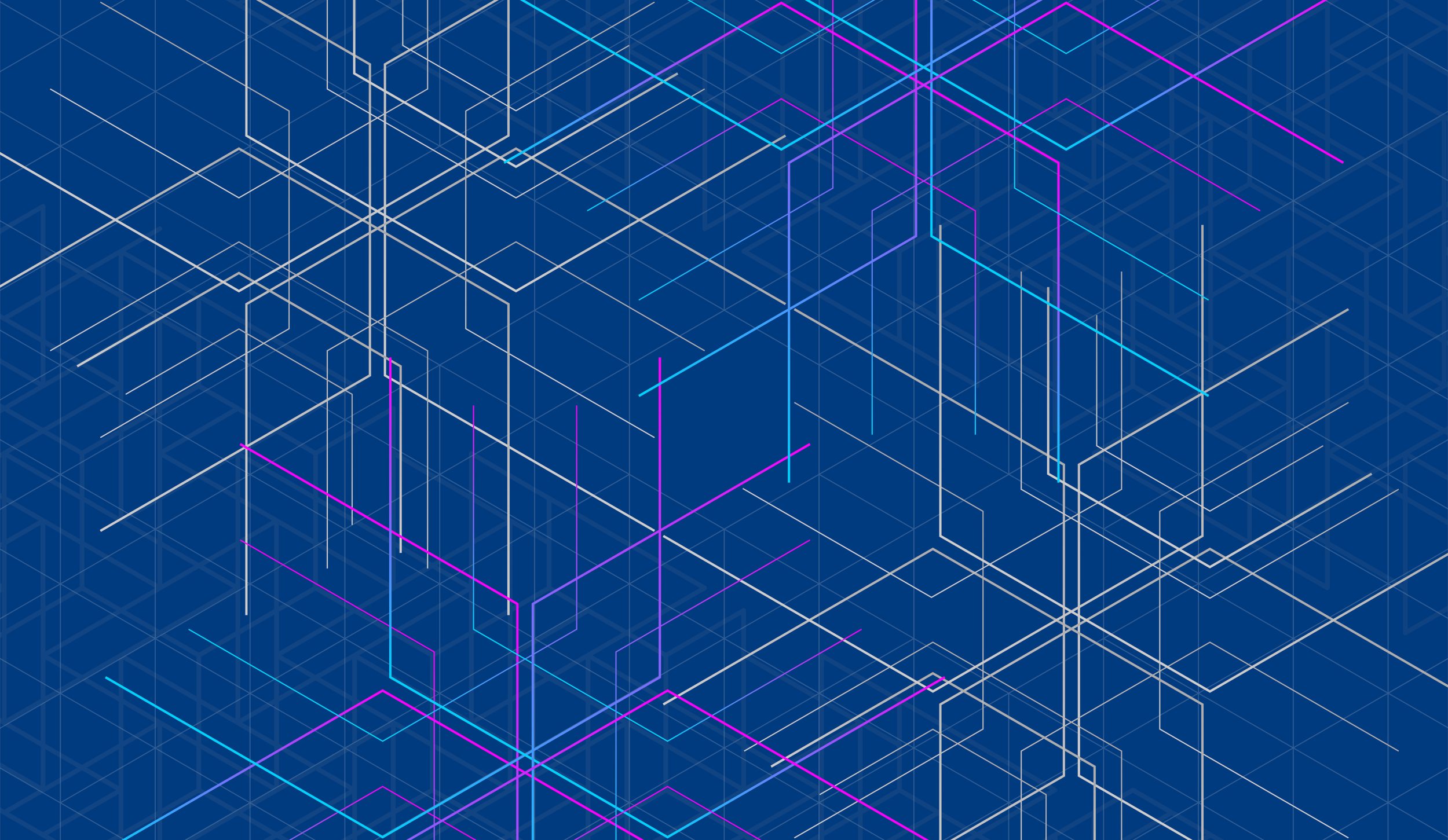
目次
- 1 ORiNの誕生と歩み:製造業界の通信標準化の起源と変遷
- 2 進化したORiN3の特徴とは?多様な機器統合を実現する設計思想
- 3 ORiN3の開発経緯と歴史的背景:なぜ生まれたのかを深掘りする
- 4 ORiN3の技術仕様と主要機能:高い汎用性と拡張性の理由を解説
- 5 ORiN3が推進するスマートファクトリーとIoT化の現実的アプローチ
- 6 導入企業が語るORiN3の導入メリットと運用効果に関する実情
- 7 ORiN3の導入事例とアプリケーション例:製造現場の成功事例紹介
- 8 ORiN3プロジェクトの全体像:産学官連携と標準化への取り組み
- 9 ORiN3の業界標準化と国際規格対応:グローバル対応の実力とは
- 10 ORiN3の今後の展望と将来性:次世代製造業を支える通信基盤へ
ORiNの誕生と歩み:製造業界の通信標準化の起源と変遷
ORiN(Open Robot/Resource interface for the Network)は、製造業界において異なるメーカーの機器や装置を統合的に管理するための通信ミドルウェアとして誕生しました。1990年代後半から2000年代にかけて、製造現場ではFA(Factory Automation)機器の多様化とベンダー依存性の高まりにより、異機種間での通信連携が大きな課題となっていました。そこで登場したのがORiNであり、日本ロボット工業会を中心とした取り組みで、その標準化が進められました。最初のバージョンであるORiN1は、主にWindowsベースのCOM/DCOM技術を利用しており、製造業における異種機器連携の第一歩を築きました。その後、より柔軟で拡張性のあるORiN2へと発展し、現在ではスマートファクトリーの中核的な通信基盤として注目されています。
製造業の異機種混在問題がORiN誕生の背景となった
1990年代の製造業界では、各ベンダーが独自の通信仕様を採用していたため、異なる装置間でのデータ共有や制御が非常に困難でした。特に、ロボット・PLC・NC装置などがそれぞれ独自のプロトコルを持つことで、システムインテグレーションの工数とコストが増大していました。このような課題を背景に、機器間の共通インターフェースを提供する仕組みとしてORiNが登場しました。ORiNは各装置の機能を抽象化し、統一された通信手段を提供することで、ベンダーや機種を問わず連携を可能にしました。この取り組みは、製造現場の生産性向上と柔軟性確保に大きく寄与しています。
ORiN1からORiN2への進化と業界への浸透過程
初期のORiN1はWindowsのCOM/DCOM技術を基盤とし、主にPCベースのアプリケーションとの連携に活用されていましたが、拡張性やネットワーク越しの接続には課題がありました。そこで、よりネットワーク対応力とクロスプラットフォーム性を重視したORiN2が開発されました。ORiN2では.NET技術やWebサービスとの連携機能が強化され、より高度な分散システムへの適応が可能となりました。これにより、製造業界では段階的にORiN2の導入が進み、標準通信ミドルウェアとしての地位を確立していきました。導入事例が増えることで、業界内の理解と活用が進み、現在のORiN3の開発へとつながっています。
日本発の通信ミドルウェアとしての国際的評価の高まり
ORiNは日本国内で誕生した技術でありながら、その設計思想の普遍性と実用性の高さから、海外でも注目される存在となっています。特に、製造業のグローバル化が進む中で、各国の工場や機器が統一された通信基盤の上で動作する必要性が増しています。ORiNは、言語や通信プロトコルの違いを吸収し、多言語・多国籍環境下での連携を可能にするため、国際的な標準化も視野に入れた活動が行われてきました。実際、IEC(国際電気標準会議)においてもその技術的枠組みが紹介されるなど、ORiNの価値は国内外で認識され始めています。
ORiNコンソーシアムによる開発と推進体制の構築
ORiNの開発と普及は、個々の企業単体では実現が難しい広範囲な連携と標準化を必要とします。そこで設立されたのが「ORiNコンソーシアム」です。この団体は、産業機器メーカー、ソフトウェアベンダー、研究機関などの協力を得て、ORiNの仕様策定やリファレンス実装の提供、教育活動などを行ってきました。これにより、各ベンダーが共通インターフェースの開発や検証を行いやすくなり、実装の互換性が保たれるようになっています。コンソーシアムの活動は、ORiNの継続的な進化と製造業界への定着を後押ししています。
ORiNがもたらした製造装置のオープン化の歴史的意義
ORiNの導入は、従来クローズドだった製造装置の世界に「オープンインターフェース」の概念を持ち込んだ点で、極めて画期的でした。多くの製造装置はベンダー依存の強いブラックボックス的な存在でしたが、ORiNの導入により、ユーザー自身が装置の情報を取得し、制御する道が開かれました。これにより、システム構築の自由度が飛躍的に高まり、製造ラインのカスタマイズや改善が迅速に行えるようになりました。また、複数ベンダーの機器を自由に組み合わせる環境が整い、製造業全体のイノベーションが促進されたのです。
進化したORiN3の特徴とは?多様な機器統合を実現する設計思想
ORiN3は、これまでのORiNシリーズの経験を活かしつつ、IoTやスマートファクトリーへの本格対応を視野に入れて開発された次世代通信ミドルウェアです。最大の特徴は、異なるメーカーや異なる通信プロトコルを採用する装置やセンサーを、単一のインターフェースで統合管理できる点にあります。設計思想としては「拡張性」「柔軟性」「高セキュリティ性」の3点が強く意識されており、産業界における標準化を強く意識した構成となっています。また、分散ネットワークに対応し、リアルタイム通信とクラウド連携を両立する構造を持ち、将来の製造現場におけるDX推進を支える通信基盤としての役割を担っています。
多階層・多プロトコル対応を実現するアーキテクチャの革新
ORiN3のアーキテクチャは、階層化された設計を特徴とし、上位アプリケーション層と下位デバイス層の間を抽象化することで、プロトコルや物理的通信手段の違いを吸収します。これにより、Ethernet/IP、PROFINET、Modbus、OPC UAなどの複数プロトコルを同一環境下で統合運用できるようになります。また、各層が疎結合で構成されているため、特定の装置やプロトコルに依存せず、新しい通信仕様やデバイスにも容易に対応可能です。この設計により、ORiN3はさまざまな機器やネットワークが混在する環境においても、高い互換性と拡張性を持って柔軟に対応できるのです。
セキュリティや冗長性など産業用途を想定した設計思想
ORiN3では、産業用通信に不可欠なセキュリティと冗長性の確保が重視されています。具体的には、TLSによる暗号化通信、認証機能、アクセス制御といった標準的なセキュリティ対策に加え、産業現場に特有の制約やリスクにも対応するための工夫がなされています。例えば、ネットワーク障害時の自動再接続機能や、フェールオーバー構成のサポート、ログ取得と監査証跡の管理といった機能が備わっており、システムの高可用性を実現します。こうした冗長化設計により、製造現場におけるトラブルの影響を最小限に抑え、運用の信頼性を確保することができます。
Webサービス連携やクラウド通信に対応した拡張性
従来のORiNではローカルネットワーク内の装置制御が主な利用目的でしたが、ORiN3ではクラウド通信との親和性が大幅に向上しています。具体的には、REST APIやSOAPベースのWebサービスとの連携が可能であり、クラウドに設置されたダッシュボードや分析プラットフォームと直接接続してデータを送信することができます。さらに、ORiN3はMQTTやHTTPといった軽量プロトコルにも対応しており、エッジデバイスからのデータ送信にも適しています。これにより、リアルタイムなデータ収集と、クラウド上での分析・制御が連携可能となり、スマートファクトリー構築の基盤技術としての地位を確立しています。
データ収集とフィルタリング機能による効率的な運用
ORiN3には、単なる通信機能にとどまらず、データの収集・整形・フィルタリングを実行する機能も組み込まれています。これは、装置から得られる膨大なデータをそのまま上位システムに送信するのではなく、必要な情報だけを抽出して送ることで、ネットワーク帯域やクラウドリソースの無駄を防ぐための仕組みです。具体的には、データのしきい値設定や変化点検出、サンプリング間隔の制御などが可能であり、現場の状況に応じた柔軟な運用が行えます。これにより、リアルタイム性を保ちつつ、システム全体の負荷を軽減し、効率的な情報活用を実現できます。
プラグイン形式による柔軟なデバイスドライバの追加対応
ORiN3では、各種産業機器に対応するためのデバイスドライバがプラグイン形式で提供されており、ユーザーは必要に応じて追加・削除・更新が可能です。これにより、新しい機器が導入された場合でも、システム全体を停止せずにドライバを追加するだけで即座に対応できるという柔軟性があります。また、サードパーティやユーザー企業が独自のプラグインを開発・配布することも想定されており、オープンなエコシステムの形成も進められています。この仕組みは、導入コストの抑制や技術的な制約の緩和に寄与し、ORiN3の普及を後押しする大きな要素となっています。
ORiN3の開発経緯と歴史的背景:なぜ生まれたのかを深掘りする
ORiN3の開発は、製造業界における急速な技術進化とIoT化の潮流に応じる形でスタートしました。従来のORiN2は、LANベースの接続とPCアプリケーションとの連携を得意としていましたが、クラウド連携やセンサーデータの収集、リアルタイム性が求められる現代のスマートファクトリーには限界がありました。こうした背景の中で、より高性能でセキュア、かつ柔軟に運用できる通信ミドルウェアの必要性が高まり、産官学連携のもとで新たに設計されたのがORiN3です。ORiN3は、産業界の標準化と技術的進化の両立を目指して開発された、次世代製造インフラの中核とも言える存在です。
製造業のスマート化ニーズがORiN3開発を加速させた
近年、製造現場では「スマートファクトリー」や「インダストリー4.0」といった概念の浸透により、センサーやアクチュエータからリアルタイムでデータを取得し、即座に制御へフィードバックを返す高度な運用が求められています。こうした環境を実現するためには、多様な機器と通信できる高度な中継基盤が不可欠です。ORiN2では限界があったクラウド接続性やプロトコル柔軟性、セキュリティなどの課題を解消する形で、ORiN3の開発が進められました。スマート化に不可欠なスケーラビリティや拡張性を兼ね備えたORiN3は、データ駆動型の製造を支える新たな基盤技術として登場したのです。
ORiN2の課題と限界が次世代開発を後押しした背景
ORiN2は製造現場における異機種連携を可能にした点で大きな功績がありましたが、インターネット通信の高速化、クラウドの活用、セキュリティ要件の強化など、環境の変化に十分に対応できていないという課題がありました。例えば、DCOMベースの通信モデルではファイアウォールの制約が大きく、クラウドやスマートデバイスとの連携が困難でした。また、スケーラビリティに乏しく、大規模工場での導入には制約があったのです。これらの限界を克服し、よりフラットで汎用的なアーキテクチャへと移行する必要性が叫ばれ、次世代仕様としてORiN3のプロジェクトが始動する運びとなりました。
政府や業界団体の支援によるプロジェクト立ち上げ
ORiN3の開発は、単なる企業内の技術開発プロジェクトではなく、経済産業省や業界団体、日本ロボット工業会などが主体となって推進された国家規模の取り組みでした。スマート製造の中核となる通信基盤の国産化と標準化を目指し、政府の支援のもとで複数の研究機関や大学、メーカーが連携して技術仕様の策定が進められました。このように公的支援が入ることで、中立性と広範な業界調整が実現され、単なる商用ミドルウェアではない「業界全体を支える共通基盤」としての性格が強まりました。ORiN3はこのような産官学連携の象徴的成果と言えるでしょう。
産業界からのフィードバックを取り入れた開発プロセス
ORiN3は、現場で実際にシステムを運用するエンジニアや企業ユーザーからの声を積極的に取り入れた、現場起点の設計思想に基づいています。開発プロセスでは、ベータ版の公開とフィードバック収集、PoC(概念実証)プロジェクトの実施を繰り返すことで、理論だけでなく実務的な有効性を重視した改良が重ねられました。例えば、「接続の簡便性」「設定の柔軟性」「障害発生時のログ取得のしやすさ」といった具体的な現場課題に対応する機能が搭載されています。こうした実践的な開発アプローチにより、導入のハードルが下がり、広範な業界への普及が加速されました。
複数ベンダー連携による共通インターフェースの実現
ORiN3は、単一企業の仕様ではなく、複数の業界リーダー企業による協力のもとで設計・実装されたという点でも注目されます。異なる機器メーカーやソフトウェアベンダーが共通のインターフェース仕様に合意し、それぞれの機器がORiN3を通じてスムーズに通信できるように設計されています。これにより、特定のベンダーに依存することなく、工場全体の設備を柔軟に構築・更新できるようになり、ユーザーにとっての選択肢が広がりました。異種機器間の統合を円滑にしつつ、長期的な運用と互換性の担保を両立したこのアプローチは、産業システムの未来において非常に重要な基盤となっています。
ORiN3の技術仕様と主要機能:高い汎用性と拡張性の理由を解説
ORiN3は、製造業における多様な装置・システムを統合的に管理・制御するための通信ミドルウェアとして、高い汎用性と拡張性を備えた仕様で構成されています。従来のローカルネットワーク中心の設計から進化し、クラウド環境やIoTデバイスとも親和性の高い通信機構を実現しました。主な技術仕様としては、マルチプロトコル対応、Webサービス連携、暗号化通信のサポート、プラグインによるドライバ追加などがあり、さらにリアルタイムデータ処理やログ管理といった運用支援機能も強化されています。これらの機能により、ORiN3は単なる「通信手段」ではなく、製造業のデジタル化を支える基盤システムとしての位置づけを確立しています。
TCP/IPベースでの通信と複数プロトコルの同時サポート
ORiN3は、通信基盤としてTCP/IPをベースに設計されており、安定したネットワーク通信と高い互換性を確保しています。これにより、インターネット越しの接続や企業内ネットワーク(イントラネット)上での利用が容易になります。また、OPC UA、EtherCAT、PROFINET、Modbus、CC-Linkなど、主要な産業用プロトコルに対応したプラグインが提供されており、ユーザーは特定のプロトコルに依存せずシステムを構築できます。複数の通信プロトコルを同時に扱えることにより、異種機器を同一のアプリケーションから統合的に制御・監視することが可能となり、システム設計の柔軟性が飛躍的に向上します。
デバイスインターフェース抽象化による機器の共通管理
ORiN3では、機器ごとに異なる制御仕様やコマンド体系を抽象化し、共通のインターフェースとして提供する設計がなされています。これにより、ユーザーは特定ベンダーのAPIに依存せず、同一のプログラミングインターフェースで複数機器を扱うことができます。例えば、ロボットアーム、PLC、センサーといった異なる種類の装置に対しても、統一的なコマンド呼び出しで制御が可能となるため、アプリケーション開発が大幅に簡素化されます。このような抽象化は、保守性や再利用性を高め、システムのライフサイクル全体を通じた効率化に貢献しています。
セッション管理機能とロギング・モニタリングの支援
産業用システムでは、接続の安定性とトラブル時の原因分析が重要です。ORiN3はセッション管理機能を備えており、各機器との接続状態を常時監視し、通信の確立・切断・再接続を適切に管理できます。さらに、ロギング機能により、機器からのデータ送受信、エラー発生時の詳細な記録を自動的に取得可能です。これらのログはモニタリングツールと連携して表示することもでき、障害発生時のトラブルシューティングを迅速化します。これにより、システムの可用性向上と運用負荷の軽減が図られ、信頼性の高い工場運用が実現します。
各種産業用ネットワークとのブリッジ機能の充実
ORiN3は、異なる産業用ネットワーク間をつなぐ「ブリッジ」としての機能も備えています。これは、たとえばOPC UAネットワークとEtherCATネットワーク間でデータを中継し、相互通信を可能にする機能です。この機能により、異なるネットワーク環境にある機器同士がデータを共有し、協調動作を行うことができます。ブリッジ機能は設定がGUIベースで行えるため、専門知識がなくても簡単に実装でき、システムの複雑さを軽減します。また、プロトコル変換やデータマッピング機能も提供されており、異種ネットワークをまたぐ統合がスムーズに行えるのが特長です。
REST APIやMQTTなどIoT向け通信規格への対応力
ORiN3は、従来の工場内ネットワークだけでなく、IoT時代に求められるインターネットベースの通信手法にも対応しています。特に、クラウド連携を意識したREST APIや、センサーデバイスからの軽量な通信に適したMQTTプロトコルをサポートしている点が大きな特長です。これにより、エッジデバイスからクラウドへのデータ転送、Webアプリケーションとの連携、スマートフォンやダッシュボードからのリアルタイム監視が実現可能となります。また、セキュリティ面でもHTTPSやトークン認証などが利用でき、安心して外部連携が行える設計となっています。
ORiN3が推進するスマートファクトリーとIoT化の現実的アプローチ
スマートファクトリーの実現には、現場の機器や装置、センサーから得られる膨大なデータを、リアルタイムかつ安全に収集・活用できる通信基盤が必要不可欠です。ORiN3は、そうした次世代工場の実現に不可欠な要素として注目されており、多様なプロトコルへの対応、クラウド連携機能、データフィルタリング能力、リアルタイム制御支援などを備えています。また、既存設備と最新デバイスの混在環境にも対応できる柔軟な設計思想を持ち、工場の部分的なアップデートや段階的なIoT導入にも適応します。結果として、ORiN3は工場全体の生産性向上、予知保全、最適化制御といった現代の製造業の課題解決に貢献する、実用的かつ信頼性の高いプラットフォームとして機能します。
スマートファクトリーにおけるデータ基盤としての機能
ORiN3は、スマートファクトリーにおけるデータ収集・統合・活用の中核的な基盤として機能します。生産設備から収集される温度、圧力、稼働状況などの情報をリアルタイムで取得し、共通フォーマットに変換してクラウドや上位アプリケーションへと送信できます。データは時系列に管理され、トレンド分析やAIによる異常検知にも活用可能です。従来は個別に構築されていた機器ごとのデータ取得システムを一本化することで、工場内の「サイロ化」問題を解消し、全体最適な生産戦略の立案が可能となります。ORiN3を導入することで、製造現場におけるデータドリブンな意思決定が現実のものとなります。
IoTデバイスとの連携を容易にする標準通信構造
現代の工場では、従来型の大型設備に加え、多数の小型センサーデバイスやIoT機器が導入されています。これらの機器は通信方式や仕様が多岐にわたるため、連携には高い技術的ハードルがあります。ORiN3では、標準化されたAPIと多プロトコル対応機能により、異なる通信方式の機器同士でもスムーズな統合が可能です。具体的には、MQTTやCoAPといった軽量通信にも対応しており、IoTデバイスから取得したデータをリアルタイムで中継・蓄積・分析する構成を容易に実現できます。これにより、エッジデバイスからクラウドまでの一貫したデータフローを構築でき、製造現場のIoT化が加速されます。
リアルタイム制御とデータ活用を両立する設計
ORiN3の大きな強みの一つは、リアルタイム性とデータ利活用の両立を可能にする設計です。たとえば、センサーからのデータをミリ秒単位で取得し、それを瞬時にPLCやロボット制御へフィードバックするといった処理が可能です。同時に、これらのデータを蓄積し、後段の分析基盤やAIエンジンに渡すこともでき、即時対応と長期的最適化の双方を実現します。リアルタイム性を確保するための優先度制御や非同期通信処理、バッファリング機能も備えており、通信の遅延や負荷集中にも強い構造です。これにより、製造ラインの高効率化と品質安定化が同時に達成できます。
工場設備のレガシー化問題への具体的な解決策
多くの製造業では、稼働年数の長い既存設備が多数存在しており、これらがIoT導入のボトルネックとなっています。ORiN3は、こうしたレガシー設備にも対応できる仕組みを提供しています。具体的には、古い機器専用の通信プロトコルにも対応するアダプタや、既存インターフェースをORiN3形式に変換するミドルレイヤーを提供しており、旧設備からでも必要なデータを抽出し、他の最新システムと統合可能です。このような設計により、大規模な設備更新を伴わずとも段階的にスマート化を進めることが可能となり、現場のコスト負担を抑えながらDXを推進する道筋を提供します。
予知保全や最適化アルゴリズムの実装支援機能
ORiN3は、単なるデータ通信基盤にとどまらず、製造現場における高度なアプリケーションの実装も支援します。とくに注目されるのが予知保全(Predictive Maintenance)への活用で、機器の稼働状況や振動・電流値などの情報を継続的にモニタリングすることで、故障兆候を早期に検知できます。また、上位のAIや統計モデルと連携するためのインターフェースも整備されており、最適化アルゴリズムの導入がスムーズです。これにより、生産性の最大化と設備の長寿命化、さらに安全性向上にもつながり、現場の価値創出に大きく寄与します。
導入企業が語るORiN3の導入メリットと運用効果に関する実情
ORiN3の導入は、企業の規模や業種を問わず、多くの現場において実際の業務改善や生産性向上に寄与していることが報告されています。そのメリットは単に「つながる」ことにとどまらず、「見える化」「最適化」「省力化」など多方面にわたります。複数の企業がベンダーをまたいだ機器の統合や、既存資産の活用、トラブル対応の迅速化、運用コストの低減などに成功しており、その成果は定量的・定性的な効果として表れています。特に、DX推進を掲げる企業にとって、ORiN3は戦略的な投資先として位置付けられており、次世代工場に必要な“柔軟で信頼性の高い中間基盤”として着実に支持を広げています。
システム統合コストの削減と開発効率の向上
ORiN3を導入した多くの企業がまず挙げるメリットは、異なるメーカーの機器を単一のプラットフォームで管理できる点にあります。従来は、機器ごとに異なるドライバやAPIを導入・開発する必要があり、システム開発には膨大な時間とコストがかかっていました。ORiN3はこれらを統一化することで、開発期間の短縮、コーディングの簡素化、テスト工数の削減を実現します。実際に、ある装置メーカーでは、従来半年かかっていた開発期間を2か月以下に短縮した事例もあります。統合コストの削減は、IT投資の回収期間を短くし、経営判断のスピードにも好影響を与えています。
ベンダーフリー環境における柔軟なシステム構築
ORiN3は、特定の機器メーカーやプロトコルに依存しないベンダーフリーな設計思想を持つため、ユーザー企業は自由に最適な機器を選定できるという利点があります。これは、急速に進化する製造技術に柔軟に対応できる大きな武器です。たとえば、ある食品加工会社では、旧式の機器と最新のIoTセンサーを組み合わせたハイブリッドな生産ラインをORiN3によって統合し、数百万円規模の新規設備投資を回避しました。このように、既存のインフラを活かしつつ、最小限の追加投資で最適なシステムを構築できる点が、ORiN3の導入を後押しする重要な要因となっています。
既存設備資産の有効活用による投資対効果の最大化
工場内には長年使われてきた装置や設備が多く存在します。これらの機器がIoT非対応であることは、スマートファクトリー化の大きな障壁となります。ORiN3は、既存設備を活かした形でIoT連携を実現できるため、設備を買い替えることなくデジタル化を推進できます。ある自動車部品メーカーでは、ORiN3を用いて30年以上稼働している装置から稼働データを取得し、AIで異常検知を行うシステムを構築。結果として、年間数百万円に相当する故障損失の回避につながりました。投資額に対して得られる効果が大きく、導入初年度で回収できた事例もあります。
異常検知やトラブル時のダウンタイム短縮事例
ORiN3の運用によって、異常検知の精度が向上し、トラブル時の対応速度が劇的に改善されたという声も多く聞かれます。ある電子部品製造工場では、機器の異常ログをリアルタイムで監視し、異常が起きた瞬間にメンテナンスチームへ通知する仕組みをORiN3で構築しました。その結果、従来は1時間以上かかっていた障害対応が、平均20分以下に短縮されました。また、ロギング機能を活用することで、トラブルの原因を即時に特定できるようになり、再発防止策の検討もスピーディに行えるようになりました。ダウンタイムの削減は、売上損失防止にも直結する重要な成果です。
現場スタッフによる運用の簡易化と業務の効率化
ORiN3は、現場のオペレーターや保全担当者が使いやすいよう配慮された設計がなされており、ノーコードまたはローコードで設定・運用が可能です。たとえば、GUIベースの設定画面を使って機器の接続状態を可視化したり、ダッシュボードからしきい値を調整したりすることができます。これにより、IT部門の支援を待たずに現場主導で改善が可能となり、業務フロー全体の効率化が進みます。実際に、ある中小製造業では、現場リーダーが自ら機器設定を変更し、ラインの生産性を15%向上させた例も報告されています。技術的ハードルの低さも、ORiN3の大きな魅力の一つです。
ORiN3の導入事例とアプリケーション例:製造現場の成功事例紹介
ORiN3は、その柔軟な設計と高い拡張性により、多種多様な業種・業態の製造現場に導入されています。導入事例を通じて見ると、従来バラバラに動作していた設備やシステムがORiN3を介して統合され、データ連携が実現したことで、業務効率や品質、メンテナンス性に大きな改善が見られたケースが多数あります。また、リアルタイム制御だけでなく、遠隔監視や異常検知、AI連携による自律化にも活用されており、単なる通信ミドルウェアを超えた「製造業の情報基盤」としての機能を果たしています。以下に代表的な活用事例を紹介します。
自動車工場におけるロボット・PLCの統合制御事例
ある大手自動車メーカーでは、溶接工程において多数のロボットとPLCが混在していたため、制御と監視の系統が複雑化していました。そこでORiN3を導入し、各機器のプロトコルを統一インターフェースで扱えるようにしたところ、工程間の同期処理が安定し、サイクルタイムが約15%短縮されました。また、リアルタイムでの状態監視が可能となり、異常発生時には即座に処理内容を把握できるようになったことで、保守対応のスピードも向上しました。この事例では、システムの統一によって開発・保守コストの削減にもつながり、年間数千万円のコスト圧縮が実現しています。
食品製造業でのIoT化による品質管理の高度化
食品業界では、製造プロセスの温度や湿度など、品質に直結するパラメータのモニタリングが重要です。ある冷凍食品メーカーでは、製造ライン各所に温度・湿度センサーを設置し、ORiN3を介して中央管理システムと接続しました。その結果、リアルタイムでの数値監視とアラート機能が実現し、温度逸脱時の即時対応が可能になりました。さらに、過去データとの比較による傾向分析も行えるようになり、製造条件の最適化や品質安定に貢献しています。この取り組みは、HACCP(食品衛生管理手法)の厳格な運用にも役立っており、監査対応の負担も軽減されました。
半導体製造現場における装置連携とトレーサビリティ確保
半導体製造は極めて高度な精密制御とトレーサビリティが求められる分野です。ある半導体工場では、複数の装置ベンダーから提供される装置が混在しており、それぞれのデータフォーマットや制御方式が異なるため、ライン全体の統一的なモニタリングが困難でした。ORiN3を導入することで、各装置からのデータを標準化し、MES(製造実行システム)とのスムーズな連携が可能になりました。これにより、製品ごとの製造履歴を一括管理できるようになり、歩留まり改善や異常時の迅速な原因追及が可能となりました。信頼性の高い品質保証体制の構築にもつながっています。
中小製造業によるエッジデバイスとクラウドの連携実現
中小企業においても、ORiN3は効果的なIoT基盤として活用されています。ある機械部品メーカーでは、IoT導入にあたってエッジデバイスを使った機器監視を試みていましたが、通信プロトコルの統一やクラウド連携に課題を抱えていました。ORiN3を採用することで、エッジデバイスから収集したデータをMQTT経由でクラウドに送信し、Power BIを用いた可視化を実現しました。これにより、工場の稼働状況をリアルタイムで本社から確認できるようになり、意思決定の迅速化と現場の改善サイクルの高速化が実現。IT部門を持たない中小企業でも、無理なくデジタル化を進められる好例です。
建設機械製造における遠隔監視とフィールドメンテナンス支援
建設機械の製造現場では、屋外で使用される機械の稼働情報や故障情報を遠隔で取得し、迅速に対応することが求められています。ある建機メーカーでは、ORiN3を利用してGPS・センサー付きの重機から運転データやエラーログを収集し、クラウドを通じてサポートセンターに送信する仕組みを構築しました。これにより、現場での状況把握が即時に可能となり、フィールドエンジニアが出動する前に部品準備や対応策の検討を済ませることができるようになりました。結果として、故障対応時間の短縮とサービス品質の向上が実現し、顧客満足度の向上にも寄与しています。
ORiN3プロジェクトの全体像:産学官連携と標準化への取り組み
ORiN3の開発と普及は、一企業や団体に閉じたものではなく、産学官が連携して進める国家的プロジェクトとして推進されています。この取り組みは、日本の製造業の国際競争力を高めるための基盤整備の一環として位置づけられており、技術開発だけでなく標準化、教育普及、国際発信までを包括的にカバーしています。多様なステークホルダーが連携し、それぞれの専門性を活かしながら持続的に進化していくORiN3は、単なる技術仕様ではなく、「産業構造そのものの変革」を促す社会基盤とも言えます。以下では、その全体像と具体的な取り組みについて掘り下げていきます。
ORiNコンソーシアムによる標準仕様策定と普及推進活動
ORiN3の仕様策定・標準化を担っているのが「ORiNコンソーシアム」です。この団体は、ロボットメーカー、ITベンダー、大学、研究機関など多様な会員で構成されており、技術委員会を中心に実装ガイドラインやAPI仕様書の策定を行っています。また、互換性確保のためのリファレンス実装の提供や、導入事例の共有、デベロッパー向けの教育支援も実施。セミナーやハンズオンなどを通じて現場の技術者への浸透を図っています。このような活動により、ORiN3はベンダーごとに仕様がばらつくことなく、統一されたインターフェースとして定着しつつあります。
大学・研究機関との連携による実証実験と技術開発支援
ORiN3の発展には、大学や研究機関の知見と技術力が不可欠です。特に、次世代通信技術やエッジAI、リアルタイムOSとの連携技術など、基礎研究と実証実験を行う場として大学との連携が進められています。たとえば、ある工科大学では、ORiN3を用いたスマート工場の模擬環境を構築し、異常検知アルゴリズムや省エネルギー制御の研究を実施。また、大学の研究成果がそのままORiN3仕様に反映されるケースも増えており、オープンイノベーションの成功事例となっています。こうした産学連携は、技術の進化と実装の迅速化を両立させる重要な要素です。
経済産業省など行政の支援による国家プロジェクト化
ORiN3は、経済産業省をはじめとする行政機関の支援のもとで推進されています。スマートファクトリーやロボット導入の拡大を目指す国家戦略において、標準通信基盤の整備は極めて重要な位置を占めており、その中核技術としてORiN3が選ばれています。たとえば、「Connected Industries」や「ロボット革命イニシアティブ」といった政府プロジェクトでは、ORiN3の活用が推奨されており、実証フィールドへの導入費用の一部補助も実施されています。こうした公的支援があることで、中小企業でも安心して導入に踏み切れる土壌が整い、全体としての導入加速に貢献しています。
他業界との共創による応用範囲の拡大と社会実装
当初は製造業向けに開発されたORiN3ですが、現在では建設、物流、医療、農業など他業界への応用も進んでいます。これを支えているのが、各業界との共創的な取り組みです。たとえば、建設現場では重機の稼働データ取得、物流業界では倉庫内の自動搬送ロボット制御、農業分野では環境制御装置の遠隔監視などにORiN3が応用されています。これにより、クロスインダストリーなデータ連携が可能になり、業界の垣根を超えたソリューション構築が実現。ORiN3は「製造業向け通信基盤」から「汎用的なインダストリアルIoT基盤」へと進化を遂げつつあります。
教育機関向けカリキュラムと技術者育成への取り組み
ORiN3の普及を持続的に進めるためには、次世代の技術者育成が不可欠です。そのため、ORiNコンソーシアムでは教育機関向けの教材提供や、技術習得カリキュラムの整備にも取り組んでいます。実際に、工業高校や専門学校、大学の情報系学科などで、ORiN3を使った実習が取り入れられており、プログラミング教育と実機制御の融合が図られています。また、企業向けにもオンライン講座や技術セミナーを定期開催しており、現場エンジニアのスキルアップにも貢献。こうした教育活動により、ORiN3の知識を持つ人材が増え、より多くの現場で導入・活用が進むサイクルが形成されています。
ORiN3の業界標準化と国際規格対応:グローバル対応の実力とは
ORiN3は、単なる通信ミドルウェアではなく、製造業界全体の共通基盤として広く採用されることを目的に設計されており、業界標準としての確立と国際的な規格対応が重視されています。日本国内においては、ロボット工業会を中心にFA分野での標準技術として普及が進められ、さまざまな業界ガイドラインにも取り上げられています。一方で、グローバル市場での競争力を高めるためには、IECなどの国際標準への準拠・連携が不可欠であり、ORiN3もそれに呼応する形で国際化が進んでいます。以下では、具体的な標準化活動の内容や国際対応の状況について詳述します。
日本国内における業界標準化の歩みと採用実績
ORiNは、1999年の初版発表以来、日本国内の製造業界で広く支持されてきました。特に、ロボット・装置のベンダー企業やシステムインテグレーターを中心に導入が進み、JARA(日本ロボット工業会)仕様の標準通信ミドルウェアとしての地位を確立しています。ORiN3では、過去バージョンの互換性を保ちながら、IoTやクラウド連携を強化するなど機能面で大幅に拡張され、さらに幅広い分野に対応できるようになりました。製造DX推進ガイドラインなどにも採用事例として掲載されており、実績ある「事実上の国内標準」として、着実に認知度と導入数を伸ばしています。
IECなど国際標準化機関との連携と参画状況
ORiN3は、国際標準化の観点からも高い評価を受けており、IEC(国際電気標準会議)をはじめとする標準化機関との連携が進められています。たとえば、IEC TC65(産業プロセス計測、制御および自動化)では、ORiNのインターフェース設計やプロトコル変換の仕組みが参考事例として取り上げられた実績があります。また、国際展示会や標準化ワークショップにおいて、日本の産業IoTの成功モデルとして紹介される機会も増えてきました。こうした取り組みは、国内外のメーカー間でのインターフェース統一に向けた基盤づくりとして重要であり、今後の標準採用に向けた布石ともなっています。
主要な産業用通信規格との互換性と相互運用性の確保
ORiN3は、業界で広く使用されている各種産業用通信規格との互換性を持ち、高度な相互運用性(インターオペラビリティ)を実現しています。具体的には、OPC UA、PROFINET、EtherCAT、CC-Link、Modbusといった主要プロトコルとの接続を可能にするプラグインが公式に提供されており、システム開発者はプロトコルの違いを意識することなく、機器間連携を実現できます。このようなマルチプロトコル対応のアプローチは、異なるメーカーの装置を混在させた生産ラインにおいて特に有効であり、装置ごとの専用ドライバやゲートウェイに依存しない柔軟な構成を構築できます。
グローバル企業による採用と海外導入事例の拡大
ORiN3は、日本国内だけでなく、アジア・ヨーロッパ・北米を中心とした海外企業への導入も進んでいます。特に、日系グローバル企業が海外拠点で統一した通信基盤として採用している事例が多く、自動車部品製造や電子機器組立の現場で活用されています。たとえば、あるタイの工場では、現地で稼働している多様なベンダーの装置をORiN3で統合し、本社のMESシステムと連携させることで、全世界の生産状況を一元管理する体制を構築しました。こうした導入事例の蓄積は、ORiN3の国際的信頼性と実用性の高さを証明しており、今後のグローバル展開における強力な後押しとなっています。
国際規格準拠を視野に入れた設計思想と今後の課題
ORiN3は当初から国際展開を視野に入れて設計されており、プロトコルの抽象化やセキュリティ要件の取り込み、言語非依存なインターフェース設計がなされています。REST APIやMQTTといったグローバルで主流となる通信方式のサポートも行われており、今後の国際標準化への対応力は十分に備わっています。一方で、現時点ではIECやISOにおける正式な規格採用には至っておらず、継続的な交渉や実証データの提示が求められています。また、国際市場では競合技術も多数存在するため、ベンチマークや事例比較の観点で訴求力を強化することが今後の課題とされています。
ORiN3の今後の展望と将来性:次世代製造業を支える通信基盤へ
ORiN3は現在、スマートファクトリーの中核を担う通信ミドルウェアとして確かな地位を築きつつありますが、その可能性はまだ発展途上にあります。今後はさらなるIoT化・AI連携・クラウド統合など、製造業の進化とともにORiN3自体も機能を拡張し続けることが求められます。加えて、国際標準への正式な対応や他産業への展開、セキュリティ要件への強化対応など、多くの取り組みが計画されています。こうした進化は、次世代製造業の競争力を支えるだけでなく、社会全体のデジタルインフラにも大きく貢献することが期待されています。
スマートファクトリーを超えたサイバーフィジカル統合の実現
今後の製造業では、物理空間と仮想空間を融合させた「サイバーフィジカルシステム(CPS)」の構築が重要になると考えられています。ORiN3はその中核となる通信基盤として、リアルタイムデータの収集と仮想空間での解析を結びつける役割を果たします。たとえば、工場内で動作する装置のデジタルツインを構築し、AIやシミュレーションエンジンを通じて未来予測や最適化処理を行うような活用が見込まれています。こうしたCPS構築に向けたデータ基盤の整備は、ORiN3の今後の技術進化の方向性とも一致しており、工場だけでなく都市インフラや交通分野への応用可能性も広がっています。
AI・機械学習との連携による自律的な製造最適化支援
ORiN3が提供するリアルタイムかつ高精度なデータ収集機能は、AIや機械学習といった高度な分析技術と非常に相性が良く、今後はAIとの密接な連携が期待されます。実際に、多くの企業がAIベースの異常検知、予知保全、最適ライン制御などに取り組んでおり、その際のデータ取得・中継インフラとしてORiN3が採用されるケースが増加しています。今後は、AIアルゴリズムの学習・推論結果をリアルタイムでフィードバックし、製造ラインを自律的に調整・最適化していくような次世代システムの中で、ORiN3が不可欠な役割を果たすと予想されます。
クラウドネイティブアーキテクチャへの進化と拡張性の確保
これからの製造業は、クラウドネイティブな設計思想をもとに、柔軟でスケーラブルなシステム構築が求められます。ORiN3もこの流れを受けて、オンプレミス環境からクラウドネイティブアーキテクチャへの進化を進めています。たとえば、ORiN3の各種機能をマイクロサービスとして分離し、Kubernetesなどのオーケストレーションツールで管理する仕組みが検討されています。これにより、大規模なスマートファクトリーだけでなく、小規模事業者にもスモールスタートが可能となり、利用範囲が拡大していくと考えられます。クラウド基盤との親和性向上は、将来的なグローバル展開にも追い風となるでしょう。
他産業・異業種への応用とクロスインダストリー化の促進
ORiN3の応用可能性は製造業にとどまりません。実際に、農業のスマートファーミング、建設現場の重機制御、物流倉庫の自動搬送システム、医療機器の遠隔監視など、他産業での活用が始まっています。今後は、業種横断的なIoT基盤としての地位を確立し、共通APIや通信インターフェースの整備によって、業界間のデータ連携やシステム統合を加速することが期待されています。たとえば、「建設×製造」「農業×ロボティクス」といった新たな連携領域においても、ORiN3の共通基盤としての価値が活かされ、社会全体のスマート化を後押しする存在になるでしょう。
国際展開と標準採用に向けたエコシステム構築の課題
ORiN3が真にグローバル標準となるためには、単に技術的な優位性を示すだけでなく、国際的なエコシステムの構築が必要不可欠です。そのためには、多言語対応ドキュメントの整備、OSSとしての一部公開、グローバルベンダーとの共同開発、導入実績の共有など、多角的な活動が求められます。また、海外の競合技術との差別化を図るためには、具体的なROI(投資対効果)やTCO(総保有コスト)削減効果の数値提示が重要です。今後、ORiN3は単なる日本発の通信ミドルウェアから、世界中の産業に共通する「グローバル産業基盤」への飛躍を目指すフェーズに入っていくことになります。